SERVICES
Oil Cleanliness Program
Our services include kidney loop oil filtrations, oil cleanliness monitoring, fresh oil filtrations, oil system flushing and comprehensive oil change solutions. For applications to gearboxes, hydraulic systems, circulating systems and heat transfer systems.
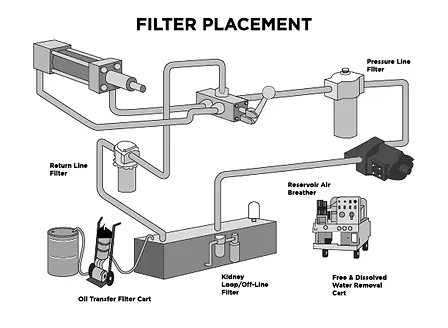
Consultations & Troubleshooting
Consult from our certified & experienced lubricant specialists on maintenance issues, machine condition monitoring and industrialized solutions. Troubleshooting issues due to temperature can be addressed through Infrared Thermography Analysis.
Lubrications & Tribology Certification Training
Training support are available for Lubrication Certification in accordance to ISO 18436-4, as well as training for KCI-MD Tribology Certification.